Девизом УГМК на «Иннопроме‑2019» стали два хэштега – #Сделано в России и #Сделано в УГМК. И действительно, УГМК, которая до сих пор позиционировала себя как компания, занимающаяся добычей сырья и переработкой металлов, на этой выставке предстала как производитель самых разных технологических новинок. Посетители «Иннопрома» могли увидеть только что запущенную в серийное производство погрузочно-доставочную машину ПДМ10‑УГМК Ferrit, созданную для проведения подземных горных работ, – ей нет аналогов в России. «Холдинг Кабельный Альянс», входящий в УГМК, демонстрировал огнестойкий кабель торговой марки «Кольчуга». Посетители «Иннопрома‑2019» могли продегустировать продукцию компании «УГМК-Агро» – мягкие сыры из козьего молока Coeur du nord, сделанные по французской технологии, а также овощи марки Mr. Green, выращенные в инновационном тепличном комплексе 5‑го поколения.
«УГМК-Телеком» представил два новых проекта с использованием искусственного интеллекта в медицине и промышленности. Один из них – система распознавания патологии легких по рентгеновским снимкам, второй – система помощи для принятия решений на производстве, которая оптимизирует расход основных технологических материалов и энергоресурсов. А Технический университет УГМК продемонстрировал свою digital-технологию для эффективного профессионального обучения. По всему было видно, что компания очень серьезно занялась диверсификацией своего бизнеса и уделяет огромное внимание высоким технологиям в самых разных сферах производства. Это и подтвердил в беседе с нашим журналистом Андрей Козицын.
– Андрей Анатольевич, какие основные события произошли в компании за последнее время?
– В части больших проектов мы запустили две современные очереди цеха электролиза меди на АО «Уралэлектромедь», огромная работа проведена по реконструкции на Гайском ГОКе – и на руднике, и на фабрике, больше 10 лет проводилась эта работа. В Башкирии достраиваем подземный рудник «Башмеди», на что понадобилось пять лет, сейчас уже стволы заканчиваем, идет подземное обустройство. Также закончена реконструкция заводов ОЦМ (по обработке цветных металлов. – «Профиль») – Кировского, самого современного из подобных предприятий по плоскому прокату, и Ревдинского, который специализируется на производстве круглого проката. Шадринский автоагрегатный завод сегодня переживает практически второе рождение – там освоили почти с нуля выпуск маневровых тепловозов – все типы тепловозов прошли сертификацию в РЖД, там же освоили выпуск и запустили в серию производство погрузочно-доставочных машин. Здесь, на «Иннопроме», можно посмотреть 10‑тонную машину, будут еще 14- и 17‑тонные, плюс самосвал для подземных работ.
– И все же главная продукция УГМК – это металлы: медь и цинк, которые очень хорошо продавались на экспорт. Изменилась ли сейчас структура потребления металлов?
– Меди мы производим около 400 тысяч тонн в год, из этого количества чуть больше половины – 220–230 тысяч тонн – уходит на внутренний рынок. К примеру, план по медной катанке на этот год у нас 170 тысяч тонн, из них 150 тысяч уходит на рынок России и стран ЕАЭС. Продукция заводов ОЦМ – порядка 50 тысяч тонн, а в пересчете на катодную медь 20–25 тысяч тонн – почти вся уходит только на внутренний рынок. Это не говоря про цинк, который практически в полном объеме находит покупателей в России.
– При таких огромных оборотах не испытывает ли компания дефицита с сырьем, то есть с медной рудой?
– Работа с сырьевой базой – это у нас постоянная тема. Основные инвестиции приходятся именно на горное производство. Как я уже говорил, это Гайский ГОК, «Башмедь», где идет строительство рудника на Юбилейном месторождении (проектная мощность 3 млн 600 тысяч тонн по руде), а также строительство рудника на Ново‑Учалинском месторождении. С этого года начинаем строительство Подольского рудника в Башкирии. Там сроки выхода на проектную мощность в 5 млн тонн руды довольно большие – около 7 лет.
– А что с цинком?
– Там все не так просто. Как вы знаете, прошлой осенью произошел пожар на заводе «Электроцинк» во Владикавказе. Сегодня этот пожар квалифицирован как поджог, расследуется уголовное дело. Можно констатировать, что этим пожаром было практически уничтожено производство цинка объемом 84 тысячи тонн в год, поэтому сейчас на рынке образовался дефицит металла. В составе нашей компании работает Челябинский цинковый завод, его мощность – 200 тысяч тонн в год, этого недостаточно, поэтому разница закрывается за счет Казахстана. Но строить новый цинковый завод мы не будем, это экономически невыгодно.
– Каковы объемы инвестиций УГМК в прошлом году, и какие планы на ближайшее будущее?
– Объемы инвестиций у нас 55–60 млрд рублей по прошлому году, примерно такие же цифры будут по текущему году. Все будет зависеть от бюджета и рынка, мы видим, что курс рубля крепнет, цены на медь уменьшаются, уголь тоже дешевеет, к тому же меняется структура потребления энергоносителей – очень многие электростанции переходят на газ, в Европе от угля вообще стараются отказаться, а экспорт на Восток ограничен возможностями РЖД, у которой сейчас пора плановых ремонтов, так что не исключена оптимизация наших инвестпрограмм в сторону уменьшения. Думаю, что это будет в пределах 10–15%. Вообще, на нашу жизнь влияет много внешних факторов… К примеру, цены на металлы будут зависеть в том числе и от того, как договорится Америка с Китаем.
– Тем не менее на этом «Иннопроме» вы подписали соглашение со Сбербанком об инвестировании в Подольский рудник достаточно серьезных средств…
– Развитие Подольского месторождения – это особая тема, там речь идет о кредите на 10 лет, и пойдет он на строительство рудника, где будет полностью подземная добыча, начиная с глубины 600 метров, стволы уходят до глубины 1000 метров, так что там предстоят серьезные затраты.
– На предприятиях УГМК вовсю идет модернизация производств. Какие планы у компании в этом направлении?
– К 2021 году мы должны закончить модернизацию медеплавильного комбината «Святогор», который находится в Красноуральске. На «Уралэлектромеди» к 2022 году должны завершить 3‑ю очередь цеха электролиза. Большие перемены ожидают наши предприятия по выпуску кабеля. Одним словом, к 22‑му году мы закончим глобальную реконструкцию на основных предприятиях. Останутся только затраты, связанные с горным производством и сырьевой безопасностью. А на них мы в год тратим примерно 500–600 млн долларов, и эти затраты никуда не денутся в ближайшие 10–12 лет. Вообще, у нас много разных проектов. Например, с углем надо будет поработать – довести его качество по зольности и калорийности до экспортных стандартов. Очень интересная тема с редкими металлами – мы производим селен, теллур, кадмий, индий, сурьму, может быть, еще один металл добавится. Все редкие металлы идут у нас с качеством «четыре девятки», как говорят металлурги. Все это хорошо продается на экспорт, а вот в самой России, к сожалению, это имеет ограниченное потребление, а ведь именно на этих металлах держится вся цифровая экономика XXI века. И на уровне мирового потребления мы обеспечиваем 10–15% редких металлов. Хочу подчеркнуть, это очень сложное и трудоемкое производство – чтобы получить, к примеру, 50 тонн теллура, нужно выкопать 25 миллионов тонн руды.
– Один из главных экспонатов нынешнего «Иннопрома» – погрузочно-доставочная машина, которую выпустил УГМК на Шадринском заводе. Что означает для вас появление такой техники, сделанной собственными силами?
– Выпуск этой машины попадает под модное нынче определение «импортозамещение», хотя на 50% детали в ней все-таки импортные, начиная с мотора. Впрочем, мотор хоть и американский по происхождению, выпускается он все-таки в Набережных Челнах. Для нас с учетом непредсказуемости курса доллара было очень важно уйти от 100‑процентной закупки подобных машин и шахтных самосвалов по импорту. Программа такая у нас есть, и она действует. Уже в этом году появится еще одна, 14‑тонная погрузочно-доставочная машина, а в следующем – первый самосвал, сделанный у нас. Затем 17‑тонная ПДМ. К 2022–2023 годам эта программа должна быть реализована, и мы сможем на 100% отказаться от импорта. Шадринский автоагрегатный завод нацелен на выпуск 50 таких машин в год. Что касается локализации производства, то мы обязательно будем повышать процент деталей, изготовленных в России, – уже сейчас идет разработка еще двух узлов, чтобы наладить их выпуск нашими силами. Думаю, цифры локализации могут достичь 60–70%, главное – найти компромисс с производителями и добиться нормального соотношения цена/качество. В любом случае уже сейчас разница в стоимости между нашей машиной и такой же импортной ощутима.
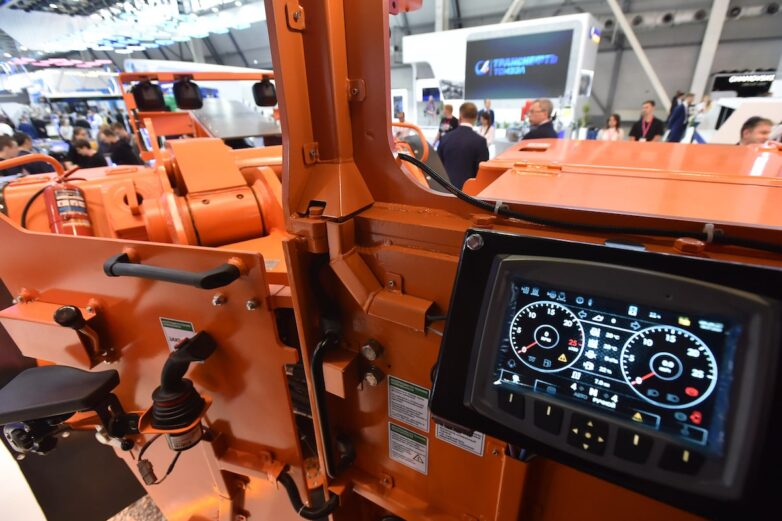
Одним из самых интересных экспонатов на выставке «Иннопром-2019» стала машина ПДМ10-УГМК-Ferrit, которая по дизайну и техническим характеристикам ничем не уступает зарубежным аналогам
Пресс-служба УГМК– Вы упомянули кабельное производство – здесь, на «Иннопроме», мы увидели совершенно новый тип кабеля «Кольчуга». В чем его превосходство над другими марками?
– Вот он в моих руках, это не просто кабель – это 100‑процентная безопасность. Это абсолютно новая продукция для нашего рынка – он прошел все испытания, получил сертификацию, начато его промышленное производство. Этот кабель обладает уникальными свойствами: он может в течение 4 часов выдерживать прямой огонь и продолжать выполнять свои функции. Это просто находка для строительной, да и не только, отрасли. Такой кабель гарантирует безопасность жилья, его можно применять на транспорте, на кораблях и даже подводных лодках. Подобной продукции на сегодняшний день нет ни у кого.
– Совсем скоро страна будет отмечать День металлурга. Что бы вы пожелали работникам вашей отрасли?
– Главное пожелание всем работникам – здоровья и чтобы наш заработок позволял достойно жить семьям металлургов и шахтеров, чтобы цены на нашу продукцию резко не падали, и тогда нам хватит и на премии, и на достойную жизнь, и на дворцы спорта, и на многое другое…