- Задачи на шесть триллионов
- Тернистый путь от простого к сложному
- Западные компании ушли по-английски
- Почему для роботов нужны люди
Задачи на шесть триллионов
О завершении работы над нацпроектами по обеспечению технологического лидерства России 20 ноября первый вице-премьер Денис Мантуров доложил президенту. По его словам, правительство в решении этой задачи взаимодействовало с регионами, бизнесом, научным сообществом. Согласованы основные приоритеты, параметры, меры поддержки и объемы финансирования.
«До 2030 года мы должны направить на эти проекты около 3 трлн рублей. Примерно такое же соотношение должно быть со стороны субъектов Российской Федерации и бизнеса. Эти объемы должны обеспечить выполнение поставленных целей развития. Это будет способствовать повышению технологического уровня социально-экономического развития основных сфер нашей страны», – подчеркнул Мантуров.
Ключевым он назвал нацпроект «Средства производства и автоматизации», который будет включать три федеральных проекта: средства производства и инструментальная промышленность, робототехника и подготовка кадров. Предстоит обеспечить технологическими решениями предприятия обрабатывающей промышленности, обновить их основные фонды.
Помимо металлообрабатывающих станков акцент решено сделать на технологическом оборудовании по аддитивным технологиям. Объем финансирования, необходимый для реализации этого нацпроекта, глава правительства Михаил Мишустин ранее оценивал более чем в 300 млрд рублей до 2030 года. Обновлять основные фонды государство поможет заводам через расширение промышленной ипотеки, субсидирование покупки станков и роботов, финансирование научно-исследовательских и конструкторских работ, льготные займы по линии Фонда развития промышленности и т. д. Многие меры господдержки работают и доказали эффективность.
«Благодаря в том числе этим решениям уже в прошлом году производство станкоинструментальной продукции в нашей стране выросло на 60%, – заявил Мишустин. – Объем выпуска металлорежущих станков в стоимостном выражении увеличился почти на 96%, кузнечно-прессового оборудования – на 370%. Хорошая динамика также сохраняется в этом году. За первые четыре месяца выпуск станкоинструментальной продукции вырос на треть».
Тернистый путь от простого к сложному
Активное развитие машиностроения в России началось в середине XIX века после ввода в строй железной дороги между Санкт-Петербургом и Москвой. Потребность в подвижном составе – паровозах и вагонах – являлась главной движущей силой создания фактически с нуля целой отрасли. Потом возник спрос на станки и оборудование со стороны судостроителей и предприятий текстильной промышленности. В результате с 1850 по 1860 год количество машиностроительных предприятий в империи выросло с 25 до 106.
Если в сельском хозяйстве выпуск базовой техники и аграрных орудий был налажен неплохо, а военные предприятия считались в техническом плане достаточно передовыми, то с обеспечением гражданской промышленности дела обстояли хуже. Только в 1870 году завод братьев Бромлей освоил выпуск простых металлообрабатывающих и деревообрабатывающих станков, сложное же оборудование шло из-за границы. В 1913-м парк станков для обработки металла в России насчитывал около 80 тыс. единиц, доля импортных составляла от 75% до 85%.
После Октябрьской революции и Гражданской войны станкостроительную отрасль пришлось создавать заново. Датой ее рождения считают 29 мая 1929 года, когда был образован Станкотрест (позднее – «Союзстанкоинструмент»). Затем приняли меры для формирования научной базы путем создания Московского станкоинструментального института (Станкин) и станкостроительных факультетов в других вузах.
Прогресс был очевиден: если в 1932-м токарные, шлифовальные и фрезерные станки выпускали восемь заводов в стране, то менее чем через 10 лет – около 40. В результате зависимость от импорта удалось снизить до 54%. Отечественное станкостроение использовало передовые мировые технические решения, поэтому советские станки могли конкурировать с ведущими западными производителями.
Появление ЭВМ и автоматики побудило СССР вплотную заняться модернизацией промышленности. Первый полностью автоматизированный производственный участок появился в 1972-м, однако переход осуществлялся заметно более низкими, чем в развитых странах, темпами. При этом зависимость от внешних поставок в станкостроении была незначительной. Доля импортных металлообрабатывающих станков в 1986 году не превышала 6% станочного парка, насчитывавшего более 7 млн единиц.
В тот период в Советском Союзе ежегодно производилось более 16 тыс. станков с ЧПУ (числовым программным управлением), около 10 тыс. промышленных роботов, 3,8 тыс. гибких производственных модулей различного назначения, 800 автоматических и полуавтоматических линий, более 180 тыс. металлорежущих станков. После 1989 года показатели резко пошли вниз, по многим видам продукции они в итоге упали до отметок, близких к нулевым.
За период политической и экономической трансформации отечественное станкостроение утратило технологический потенциал, цепочки поставок разрушились, отсутствие научной и кадровой поддержки остановило новые разработки. Последнее означало, что отрасль стала неконкурентоспособной и больше не могла отвечать реальным запросам предприятий. Они были вынуждены искать альтернативных поставщиков за границей.
К 2014-му зависимость от продукции зарубежных партнеров достигла 80%, в гражданских отраслях – еще выше. Мощности станкостроительных заводов упали на 75% от уровня 2000 года, а выпускаемая продукция в большинстве случаев не отвечала запросам потребителей по функционалу и качеству. Фактически станкостроение в РФ было отброшено почти на полтора века назад, вернувшись к производству простых станков.
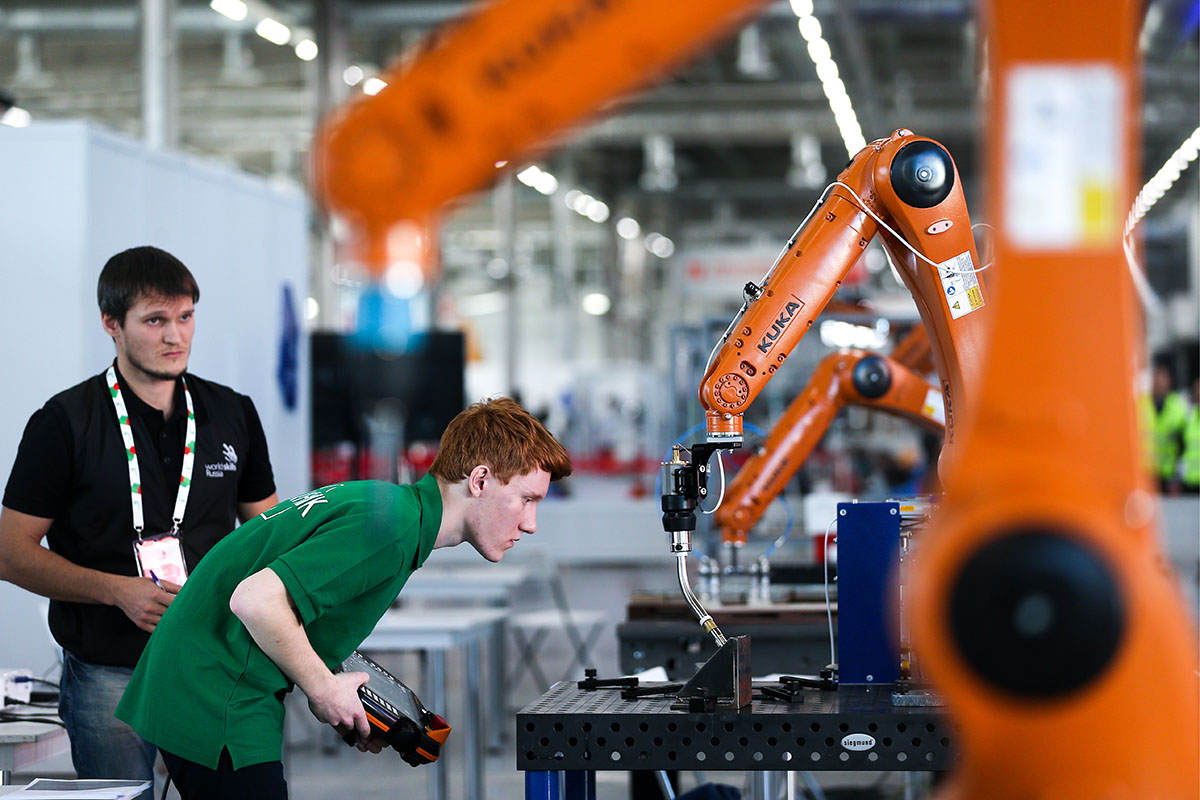
В России насчитывается около 200 станкостроительных предприятий
Егор Алеев/ТАССЗападные компании ушли по-английски
Тревожный звонок прозвучал вместе с первыми санкциями 2014 года, когда на некоторых предприятиях, в том числе сектора ВПК, так называемое подключенное оборудование внезапно остановилось, выдавая сигнальные сообщения о невозможности дальнейшей эксплуатации. Именно в этот момент встал вопрос о программе импортозамещения в станкостроительной отрасли. Зарубежные станки было крайне сложно обслуживать из-за отсутствия специалистов, технической поддержки, нехватки запчастей, невозможности обновления программного обеспечения (ПО).
За пять лет особого прогресса в импортозамещении станкостроителям достичь не удалось. Объемы выпуска простых металлообрабатывающих станков хотя и удвоились (с 4200 единиц в 2013 году до 9100 в 2019-м), но в полной мере спрос не удовлетворяли. В 2013 году заводы РФ приобрели 16 700 таких станков, в 2019-м – 23 100.
Иная картина с переходом на отечественное ПО. Здесь российские разработки уверенно отвоевывают рынок. Принятые в декабре 2022-го дорожные карты «Новое индустриальное программное обеспечение» и «Новое общесистемное программное обеспечение» предусматривают, что к 2030 году доля отечественного ПО в сфере автоматизации вырастет до 90% (с 41% в 2021 году), в сфере интернета вещей – до 76,8% (с 41,5% в 2021-м), в сфере ERP-систем (унифицированные системы автоматического учета и контроля числовых метрик предприятия) – до 92,3% (с 78,5% в 2021-м).
После введения в 2022 году многочисленных санкций со стороны США, Евросоюза и их союзников отечественные промышленники начали искать обходные пути завоза критически важных станков и оборудования. На основе данных Центробанка можно сделать вывод, что самая высокая доля импортного оборудования – в металлургии, легкой промышленности, деревообработке, фармацевтическом производстве. Поначалу большинство проблем решал параллельный импорт, однако затем каналы поставок перекрыли, и предприятия сосредоточили внимание на китайской продукции.
Санкционные ограничения подсветили зависимость от зарубежных поставок не только промышленных предприятий в целом, но и станкостроителей в частности. Во многих случаях на поверку из отечественного в российских станках – только металлоконструкция, а до 95% начинки (электроника, кинематика, гидроузлы) – импортные.
Одним из косвенных маркеров проблем станкостроительной отрасли РФ является валовое производство подшипников. В нашей стране их изготавливают около 100 млн штук в год. Для сравнения: в Японии – более 5 млрд штук. При этом в России полностью отсутствует производство подшипников, выдерживающих несколько десятков тысяч операций без существенной потери ресурса.
Почему для роботов нужны люди
Конечно, сегодня в мире вряд ли найдется хоть один производитель станков, обходящийся без чужих деталей, но принципиальное значение имеет уровень импортозависимости. Например, в Плане мероприятий по импортозамещению в станкоинструментальной промышленности на период до 2024 года из всего списка продукции самый высокий плановый показатель доли отечественной продукции на 2024 год составляет 50% (неэлектрическое оборудование для пайки и/или сварки). Остальные – в диапазоне от 15% до 45%.
В России насчитывается около 200 станкостроительных предприятий, однако крупных и средних из них не более трех десятков. В Стратегии развития отрасли на период до 2035 года, утвержденной в ноябре 2020-го, в качестве целевых ориентиров названы: рост производства продукции на 5,7% в год, до 79,5 млрд рублей; увеличение локализации до 70%; наращивание экспорта до 16,5 млрд рублей.
Документ, как представляется, придется актуализировать после принятия нацпроекта «Средства производства и автоматизации». Дефицит кадров – один из вызовов. В короткие сроки подготовить в нужном количестве специалистов, разбирающихся в современных станках или промышленных роботах, крайне сложно. Для обучения сначала необходимо создать современную техническую базу в учебных заведениях.
Отсутствие собственных научно-технических разработок или хотя бы научного задела – еще одно серьезное препятствие. Сложное станкостроение или промышленная робототехника исторически не были нашей сильной стороной, как не было и полноценного крупносерийного производства такого оборудования, за исключением отдельных продуктов для атомной промышленности и ВПК. Между тем обстоятельства вынуждают нас ликвидировать отставание и обеспечить технологический суверенитет.
Автор – завкафедрой предпринимательства и логистики РЭУ им. Г.В. Плеханова