Чудеса из принтера
Технология 3D-печати не совершила революцию на Земле, но обещает прорыв в космосе
Октябрь 2019‑го стал месяцем громких событий в сфере 3D-печати. Северо-Западный универ-ситет (Чикаго, США) представил прототип принципиально нового принтера, работающего быстрее и точнее существующих аналогов, а в Университете штата Мэн напечатали крупнейший монолитный объект в истории – 7‑метровую лодку.
Сообщения о рекордах 3D-печати и заверения в ее радужных перспективах появляются в СМИ с завидной регулярностью. Однако эту технологию трудно назвать новинкой: так называемое аддитивное производство известно с середины 1980‑х. Тогда, в рамках «индустрии 3.0», и сегодня, когда на подходе уже «индустрия 4.0», она остается нишевым решением для некоторых производственных сфер.
Обещанной футурологами революции не случилось: мы не распечатываем на домашнем принтере еду, одежду и таблетки, фабрики не закрылись за ненадобностью, всеобщая доступность материальных благ не пошатнула мировую экономику.
Вместе с тем сегодня 60–80% крупных предприятий уже используют 3D-принтеры в технологических процессах, хотя и не отказываются от традиционных методов производства там, где это экономически выгоднее. Новые проекты в медицине и космонавтике возлагают на 3D-печать большие надежды – вплоть до того, что ее называют шансом человечества на освоение дальнего космоса и долголетие без болезней. Так ли это, «Профиль» разбирался вместе с представителями бизнеса, которые уже применяют перспективную технологию.
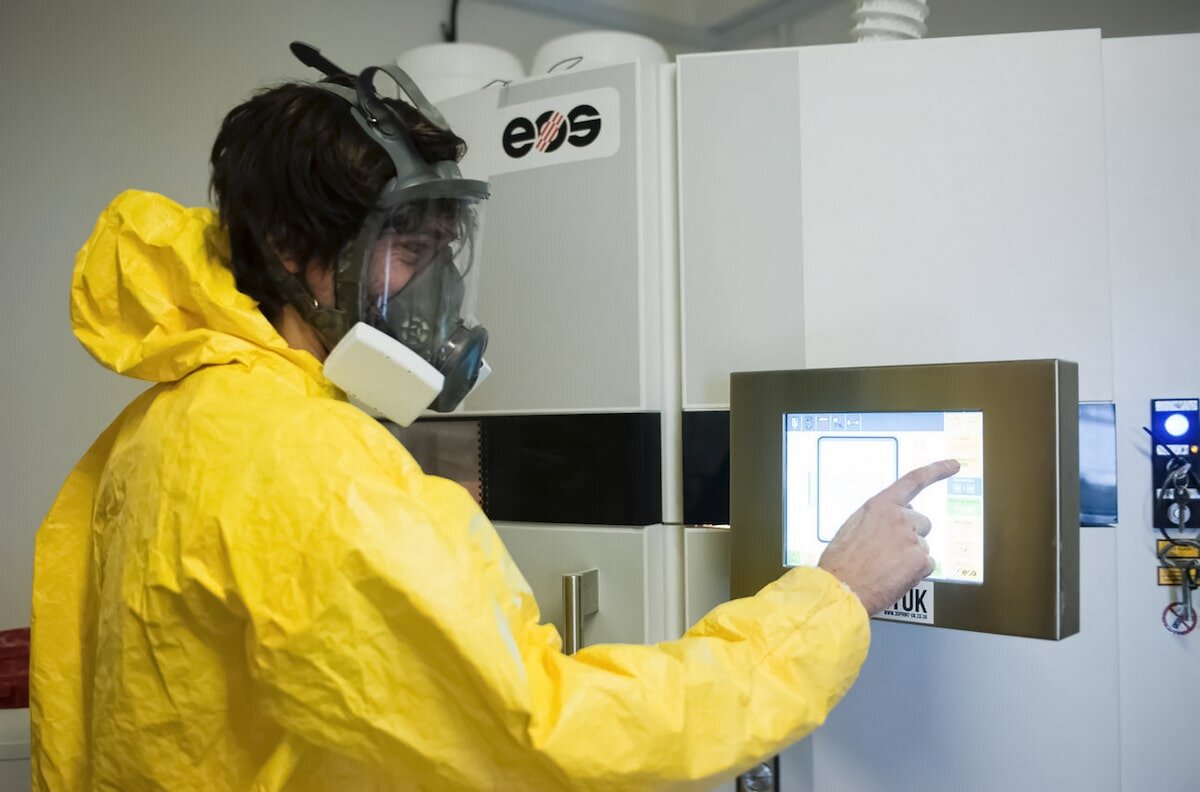
На 3D-принтере можно напечатать как сложные детали самолетов, так и декоративные безделушки. В зависимости от сценария печати объект высотой 10 см может иметь от 250 до 1000 слоев
Piero Cruciatti / Vostock PhotoПорошок, смола и пластик
Печать любого 3D-объекта начинается с компьютерного моделирования: принтеру надо знать, что создавать. Современные технологии позволяют моделировать трехмерные объекты с нуля в специальных программах (самая популярная – AutoCAD) либо сканировать реальные предметы с помощью камер и датчиков. Сегодня в интернете можно найти уже готовые библиотеки: по запросу «модели для 3D-печати» Google выдает целый список ресурсов с платными и бесплатными файлами в формате STL.
Мощность компьютеров и точность датчиков – первая преграда, долгое время стоявшая на пути развития аддитивных технологий. Если сегодня качественную 3D-модель можно сделать на ноутбуке средней мощности, то в 1990‑х для этого требовались сверхпроизводительные и крайне дорогие компьютеры. Подешевели 3D-сканеры: самые доступные можно купить за 20–30 тысяч рублей, цена продвинутых, подходящих для крупных и сложных производств, колеблется в районе 1 млн рублей. А простые 3D-модели сегодня могут создавать даже камеры смартфонов – на аппаратах Apple это позволяет делать приложение STL Maker.
После того как модель создана, ее можно печатать, выбрав материал под конкретную задачу. Браслет на руку или декоративную фигурку можно напечатать из дешевого и яркого пластика, тогда как для ракетных компонентов нужны куда более крепкие композиты. Каждый материал требует индивидуального подхода, что обусловливает наличие разных техник 3D-печати.
Одним из самых многообещающих способов считается стереолитография. В специальную ванну с прозрачным дном заливается фотополимер – жидкое вещество, как правило, смола, которая меняет свойства под воздействием света. Снизу направляются сфокусированные ультрафиолетовые лучи, которые заставляют полимер твердеть в нужных местах. Получается верхний слой будущего 3D-изделия. Затем ванна немного опускается, и лучи «вырисовывают» второй слой, затем – третий и так далее, до тех пор пока не получится готовый предмет.
Другая часто используемая технология – спекание. Оно позволяет распечатать предметы из традиционных материалов: различных металлов и сплавов (титан, алюминий, сталь), термопластика, керамики. Материал в форме порошка распыляется тонким слоем на поверхности принтера, после чего лазером «выжигается» нужный слой будущего объекта. Сверху наносится новый слой порошка, операция повторяется. Так слой за слоем создается «запрограммированный» в STL-файле предмет.
Фотополимерные и лазерные 3D-принтеры предназначены для сложных и дорогостоящих производств и стоят сотни тысяч, зачастую миллионы рублей. Но в магазинах техники можно найти и более простые модели стоимостью от 20 тысяч рублей. В продаже стали появляться даже 3D-ручки – портативные принтеры, позволяющие «рисовать» объекты от руки прямо в воздухе. В основе этой технологии лежит экструзионная печать: легкоплавкий пластик в форме толстых нитей подается в камеру, где плавится до жидкого состояния (при температуре около 200 градусов) и выдавливается через сопло. Затем при комнатной температуре вновь застывает в нужной форме. Правда, таким способом получить надежные компоненты сложно: точность печати будет невысокой, а при интенсивной нагрузке пластик может расплавиться из-за нагрева.
В зависимости от сценария 3D-печати объект высотой 10 см может иметь от 250 до 1000 слоев, а на его печать могут уйти как считанные минуты, так и несколько часов (не считая времени разработки электронной модели). Возможно, теперь процесс ускорится. В октябре Северо-Западный университет (Чикаго) сообщил о создании прототипа 3D-принтера HARP, который по принципу стереолитографии может печатать до 46 см объектов за один час на рабочей площади 2300 см2. Причем одновременно может изготавливаться несколько независимых друг от друга деталей. Добиться такого результата позволила продвинутая система охлаждения с помощью жидкого тефлона, которая на высоких скоростях печати не дает конструкции деформироваться из-за слишком высокой температуры.
Отправлено на принтер
Чем полезна 3D-печать на практике? Как выяснил «Профиль» из бесед с руководителями компаний, решивших внедрит аддитивные технологии, она экономить время и производственные мощности на создание сложных механизмов.
Генеральный менеджер Siemens Digital Industries Software в России и СНГ Виктор Беспалов приводит в пример производство газовых горелок: «Вместо сборки из 13 деталей сейчас конструкция состоит из одной детали, срок производства сокращен с 26 до 3 недель, на 22% снижен вес конструкции». В итоге производитель не только сократил расходы на производство, но и повысил надежность продукции, поскольку сборный механизм из 13 деталей намного вероятнее выйдет из строя, нежели цельный объект.
Как отмечает Максим Семенов, руководитель отдела продуктового менеджмента департамента промышленного и бытового оборудования «Грундфос», 3D-печать позволяет во многих случаях отказаться от дополнительных технологических операций – расточки, сверления, фрезерования. «В итоге можно создавать изделия с более сложной геометрией и дизайном, соединять в одной детали те компоненты, которые традиционным способом совместить невозможно», – говорит он.
Также 3D-принтеры упростили создание опытных образцов (прототипов), а значит, и вывод новой продукции на рынок. «Конструкторы и дизайнеры получили возможность быстро проверить изделие на собираемость, эргономику, оценить дизайн», – объясняет гендиректор Инжинирингового центра аддитивных технологий «Ростеха» Александр Давиденко. «Это позволяет быстрее модернизировать конструкцию существующих продуктов и повышает темпы импортозамещения», – добавляет начальник конструкторского отделения НПП «Рубин» (холдинг «Росэлектроника») Александр Кашаев. «30 лет назад на изготовление прототипа у нас уходило 4–5 недель, 20 лет назад – 4–5 дней. Сегодня это занимает всего 4–5 часов», – радуется Максим Семенов.
Конкретный способ 3D-печати зависит от сферы применения. Так, экструзионный принтер не годится для сложных производств, но позволяет создавать необычные украшения и предметы интерьера – например, органайзеры. Это вариант для дизайнерских студий и магазинов хендмейда: при относительно небольших затратах можно создавать продукцию на заказ, которую не купишь в обычных супермаркетах. Такие принтеры годятся и для домашнего использования, если, конечно, покупатель готов потратиться на устройство размером с две микроволновки, которое используется далеко не каждый день.
Самое креативное применение 3D-печать нашла в сфере образования – в школах и в кружках для юных техников. «При помощи 3D-моделирования дети создают собственных роботов любых форм и конфигураций, различные детали и заготовки. Они просчитывают каждую мелочь, учатся применять допуски, считают погрешности, развивают пространственное мышление», – рассказывает основатель компании ROBBO Павел Фролов.
Что касается дорогих 3D-принтеров, работающих по принципу стереолитографии или лазерного спекания, то они востребованы в медицинской, автомобильной, авиационно-космической отраслях. «С помощью 3D-печати мы отрабатываем новую конструкцию авиационного двигателя, – делится гендиректор АО «ЦАТ», эксперт «Ростеха» Владислав Кочкуров. – Мы должны научиться производить аддитивным методом 20% массы двигателя. Это повысит его топливную эффективность и сделает легче весь самолет».
Александр Давиденко приводит в пример стоматологию, где зарекомендовала себя технология лазерного плавления металлических порошков. Она позволяет создавать коронки, каркасы протезов, ортодонтические аппараты и другие изделия сплавов быстрее, точнее и дешевле, чем методом литья и фрезерования. Для получения электронной модели имплантов используются высокоточные трехмерные сканеры.
Особняком стоит кулинария. На пищевых 3D-принтерах можно быстро напечатать красивые, нестандартно выглядящие десерты, для которых в ином случае нужна сложная производственная линия. Главное – иметь электронную модель и все необходимые ингредиенты. Кроме того, технология может пригодиться там, где без нее действительно не обойтись. Например, немецкая компания Biozoon Food Innovations разработала принтер блюд для людей, которым тяжело пережевывать твердую пищу.
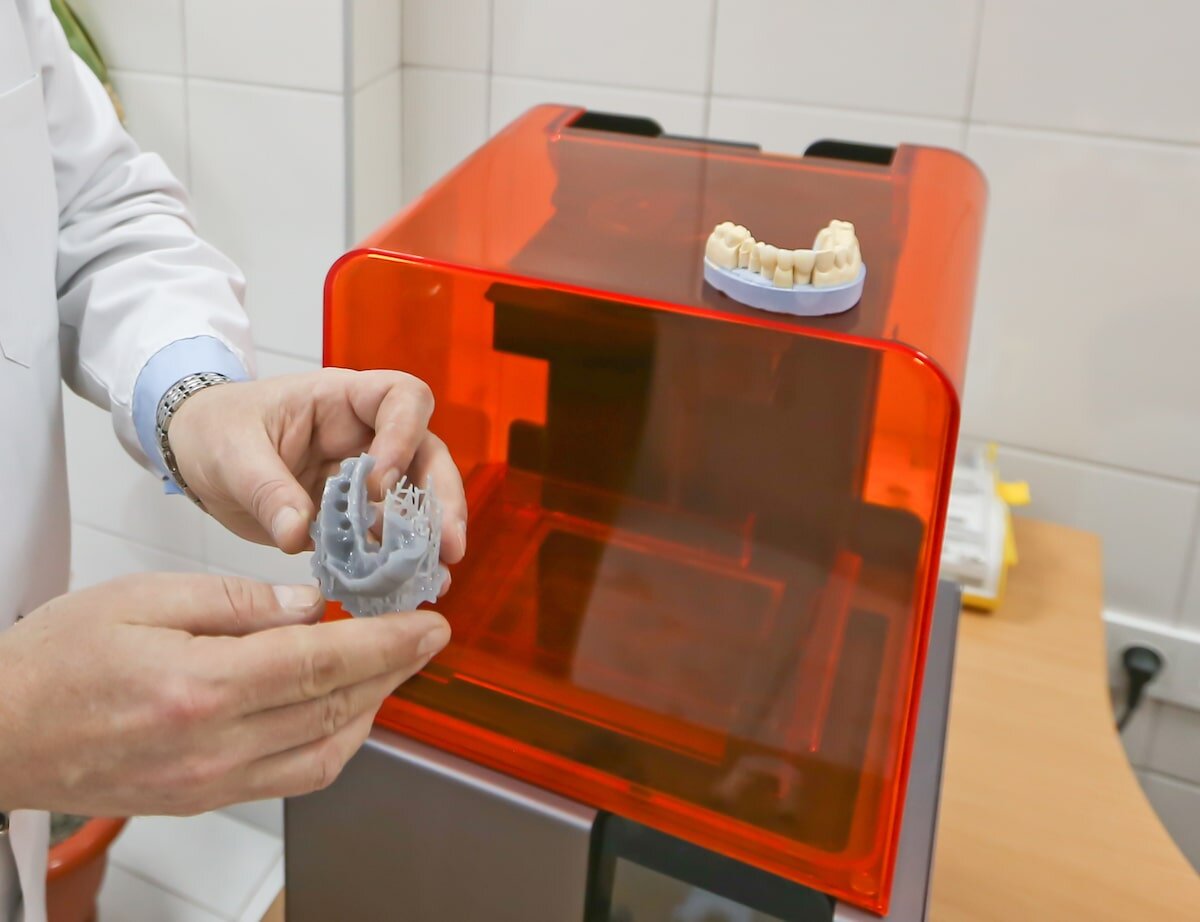
Выгода от использования 3D-печати проявляется при штучном производстве, например, стоматологических протезов. Редактируя виртуальную модель, можно адаптировать изделие для нужд конкретного клиента
Scharfsinn / Alamy / Vostock PhotoПолезная альтернатива
Как утверждается в исследовании Ernst & Young, сегодня 65% компаний используют аддитивные технологии. Лидерами являются высокотехнологичные Южная Корея (81%) и Китай (78%). Впечатляющий показатель, но нужно понимать, что «использовать» не равно «внедрить везде и повсюду». За 30 лет своего существования 3D-печать не вытеснила традиционную, более трудоемкую механическую обработку, а стала лишь дополнительной опцией на производстве. Почему?
Главной причиной эксперты «Профиля» называют высокую стоимость оборудования и расходных материалов: хоть она и снижается, до ценового паритета еще далеко. «Напечатанная на 3D-принтере деталь может стоить 300 евро, а такая же, созданная с помощью литья под давлением, – 1 евро», – объясняет Семенов.
Экономическая выгода появляется лишь там, где речь идет не о серийном, а о штучном производстве и каждый экземпляр требует перенастройки оборудования. В этом случае подготовка фрезеровочных и литьевых станков затратнее, чем редактирование виртуальной модели изделия.
Другим препятствием на пути 3D-печати остается консерватизм на предприятиях. Отказаться от проверенных годами технологий в пользу новых и весьма недешевых не так-то просто. «Закупки оборудования недостаточно, нужно говорить об изменении мышления инженеров‑конструкторов и производственников», – признает Владислав Кочкуров.
Иногда звучат требования законодательно ограничить применение 3D-печати как небезопасной технологии. Тут действительно есть над чем задуматься. 9 октября в немецком городе Галле были застрелены два человека из пистолета, напечатанного дома на 3D-принтере. Оружие неоднократно заклинивало, в противном случае жертв было бы больше, но факт налицо: распечатать огнестрел дома может любой желающий. В июле 2018‑го в США разрешили свободно публиковать в интернете файлы, позволяющие распечатать пистолет Liberator. Его практически полностью можно изготовить из пластиковых деталей, металлическим должен быть только боек.
Распечатать будущее
Предполагается, что в будущем аддитивные технологии обеспечат развитие медицины и космонавтики, позволив человеку жить дольше и улететь дальше, чем сегодня. Так, ожидается трансформация донорского рынка. В лабораториях уже сумели наладить печать кровеносных сосудов и даже функционирующих органов. А в апреле 2019 года израильские ученые из человеческих тканей распечатали миниатюрную модель сердца. Похоже, киберпанковым антиутопиям не суждено сбыться: в будущем человечество будет имплантировать себе не металлические органы, а распечатанные на принтере из своих же собственных тканей, чтобы организм не отвергал.
Что касается космоса, то на МКС сегодня находится несколько экспериментальных принтеров, печатающих в условиях нулевой гравитации. С одной стороны, это усложняет механизм принтера в целом: ему требуется магнитно-акустический излучатель, который направляет рабочий материал в нужные точки трехмерной камеры. С другой – снижается риск поломки конструкции, а значит, можно создавать более сложные предметы.
Один из таких принтеров принадлежит компании Made in Space и был установлен еще в 2014 году. Через несколько лет компания, усовершенствовав работу устройств в невесомости, планирует запустить принтер в качестве самостоятельного спутника, который сможет печатать компоненты прямо на орбите. А в конце 2018 года NASA отправило на МКС «Рефабрикатор» – устройство, использующее для печати переработанный пластик. В будущем такие аппараты смогут использоваться на Земле, что дает надежду на частичное решение проблемы пластикового загрязнения планеты.
Российский сегмент старается не отставать от зарубежных коллег: в прошлом году на МКС отправился 3D-биопринтер «Орган.Авт» – разработка российских компаний «Инвитро» и 3D Bioprinting Solutions. Недавно он напечатал из клеток мышечной ткани коровы небольшой, диаметром всего несколько миллиметров, кусочек мяса.
Преимущество технологии заключается в том, что клетки могут размножаться, для чего им требуется небольшое количество ресурсов, в основном воды. Таким образом, по мнению инженеров, можно из 100 отправленных в космос клеток получить около 100 миллионов и решить вопрос питания космонавтов. А затем массовое распространение технологии избавит человечество от необходимости убивать животных для получения полноценного мяса. Эксперименты с «Орган.Автом» на МКС планируется проводить до 2024 года.
На 3D-печать возлагаются надежды и в деле дальнейшего продвижения человека во Вселенной. В 2015 году выходцы из Blue Origin и SpaceX основали стартап Relativity Space для аддитивного производства ракет. Инженеры компании полагают, что с помощью этой технологии сумеют сократить количество деталей ракеты более чем в сто раз. На строительство одной ракеты при этом должно уходить 60 дней против года-полутора классическим способом. Ожидается, что стоимость ракеты Terran 1, способной выводить 1250 кг полезного груза на орбиту, составит $10 млн. Компании уже удалось привлечь $185 млн инвестиций, а осуществлять коммерческие запуски предполагается с 2021 года: Relativity Space будет выводить на орбиту небольшие телекоммуникационные спутники.
Но и это не все. Сборные 3D-принтеры называют одной из главных технологий, благодаря которой станет возможна постройка колоний на Луне, Марсе и других небесных телах. Вместо того чтобы отправлять в далекое путешествие полностью готовые конструкции, такой принтер сможет строить здания из местного материала – реголита или марсианского песка. Правда, это пока из области фантастики: печатать полностью монолитные дома не научились даже на Земле. На данный момент самый крупный объект, целиком изготовленный на 3D-принтере, – 7‑метровая 2,2‑тонная лодка 3Dirigo, представленная сотрудниками Университета штата Мэн в октябре. На то, чтобы целиком ее распечатать, ушло 72 часа.
При этом дома, собранные из отдельных компонентов, напечатанных аддитивным способом, уже не редкость. В 2016 году в Дубае таким образом было построено небольшое офисное здание. 17 дней заняла печать его деталей на гигантском (6х12х36,5 м) 3D-принтере. Еще два дня длилась сборка, после чего три месяца шли монтаж коммуникаций и отделка интерьера. Технология позволила вдвое сократить срок строительства, но принцип не изменился: для такого проекта недостаточно одного принтера, требуется полноценная строительная инфраструктура (подъемники, погрузчики и т. д.). Ни то, ни другое отправить на другую планету сегодня невозможно.
В исследовании Ernst & Young говорится, что аддитивное производство начнет заметно вытеснять традиционное в районе 2030 года. То есть мгновенной революции ждать не стоит. Но рано или поздно 3D-печать изменит нашу жизнь до неузнаваемости.
3D-печать: хронология
1968 год
Разработана первая технология в системе CAD/CAM, которая в будущем станет стандартом для 3D-печати.
1974 год
Британский химик Дэвид Джонс в журнале New Scientist впервые описал идею 3D-печати. Тогда она выглядела чистой фантастикой.
1983 год
Чарльз Халл представил практическую концепцию 3D-печати. Первым напечатанным объектом стал небольшой стаканчик.
1986 год
Халл получил патент на новую технологию и основал компанию 3D Systems.
1988 год
Американский инженер Стивен Скотт Крамп разработал концепцию экструзионной печати, которая сегодня применяется в бюджетных 3D-принтерах.
1992 год
Компания Крампа Stratasys выпустила в продажу первый коммерческий экструзионный 3D-принтер.
1995 год
Исследовательская команда Fraunhofer Society разработала технологию 3D-печати с помощью лазерного спекания.
1999 год
В Институте регенеративной медицины Wake Forest впервые имплантировали человеку напечатанный на 3D-принтере орган – мочевой пузырь.
2000 год
Инженер Техасского университета Томас Боланд впервые использовал основанные на живых клетках «биочернила» для печати тканей человеческого организма.
2005 год
Итальянский инженер Энрико Дини запатентовал технологию D‑Shape, позволяющую печатать компоненты для зданий на принтере размером 6x6x3 м.
2012 год
Ученые из университета Пенсильвании и Массачусетского технологического института впервые напечатали искусственный орган – печень.
2014 год
На МКС отправлен 3D-принтер, способный печатать в условиях невесомости.
2015 год
В Шанхае компанией WinSun возведены первые дома, все строительные компоненты которых напечатаны на 3D-принтерах.
2017 год
Успешно запущена ракета Electron американской компании Rocket Lab, двигатель которой практически полностью напечатан на 3D-принтере.
2019 год
Ученые из Тель-Авивского университета напечатали миниатюрную (2,5 см в диаметре) модель живого сердца.
Читайте на смартфоне наши Telegram-каналы: Профиль-News, и журнал Профиль. Скачивайте полностью бесплатное мобильное приложение журнала "Профиль".